
This exponential relationship is what makes STM sensitive enough to resolve individual atoms, even under ambient conditions. If the tip moves closer to the sample surface, the tunneling current increases exponentially. By measuring the Z-axis voltage as a function of scan position, an image of the sample topography is constructed. The X and Y axes of the scanner are used to raster scan the tip across the sample. The tunnelling current measured by the transimpedance amplifier is fed into a feedback loop which controls the voltage applied to the Z-axis electrode of the piezo scanner and acts to maintain a constant tunneling current, and therefore a constant tip-sample distance. The STM tip is mounted on a piezoelectric scanner, which is capable of sub-angstrom motion in all directions. If the gap is small enough (<1 nm), electrons can cross the gap via quantum tunneling. This “tunneling current” is typically in the pA – nA range, and can be measured with a transimpedance amplifier. STM is a tool capable of imaging surfaces with atomic resolution. In STM, a sharp metallic needle is brought within a few angstroms of the surface of a conductive sample and a small bias voltage is applied across the gap. Turns out I was able to image highly-oriented pyrolytic graphite (HOPG) with my STM with atomic resolution! The image below shows the hexagonal lattice structure of graphite.
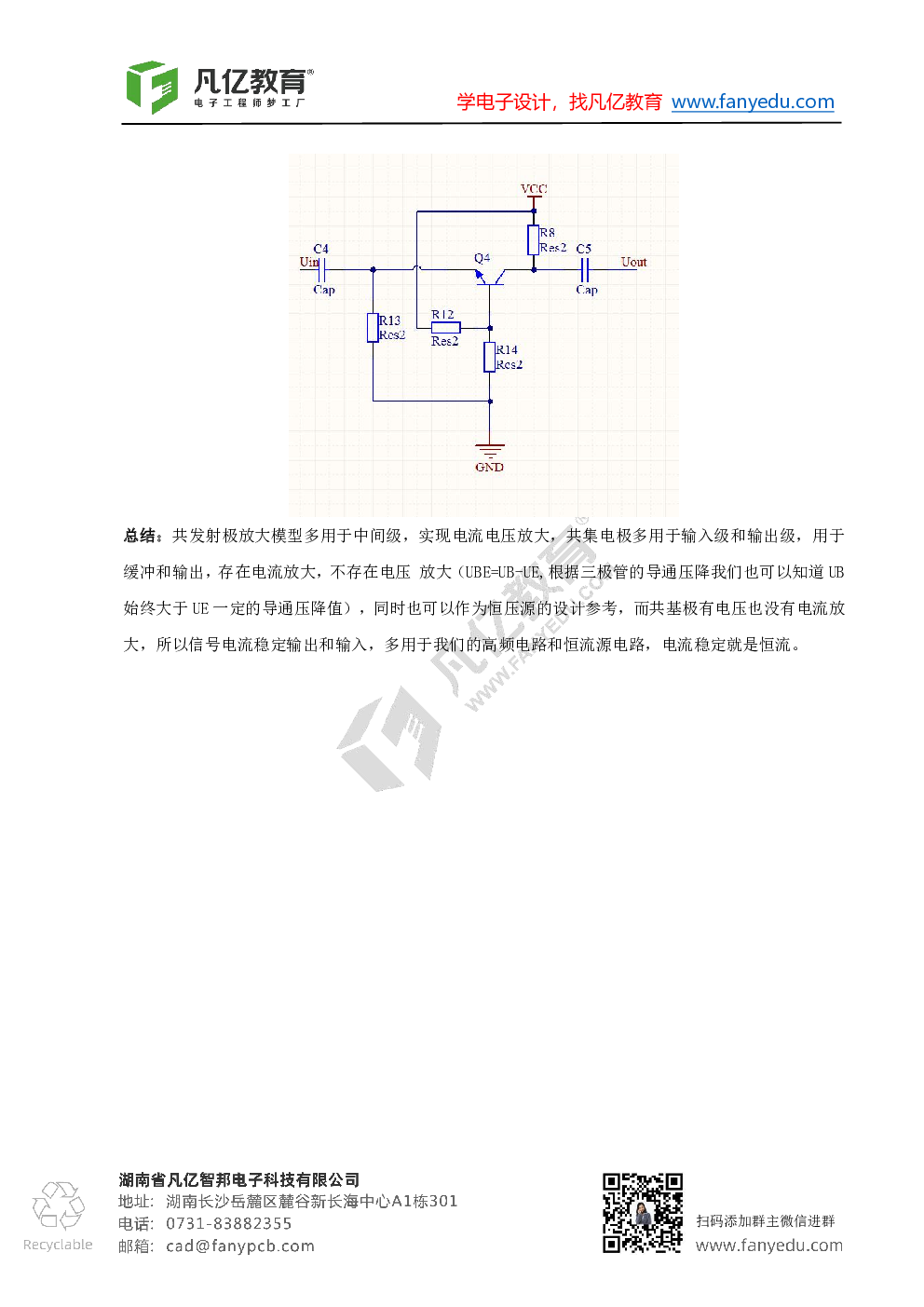

This type of scanner is less rigid than what is usually used for STM, but I decided to give it a try and see how far I could get with it. This project is my attempt to build a low-cost scanning tunneling microscope (STM) capable of atomic resolution imaging in air. The piezo scanners typically used in STM typically cost at least hundreds of dollars. Some time ago I came across John Alexander’s simple STM project, in which he used a cheap piezo buzzer element with one of the electrodes cut into quadrants to enable XYZ motion.
